1. The three key policy interest rates "cut interest rates" on the same day.
The central bank yesterday carried out a 7-day reverse repurchase of 204 billion yuan, and the winning bid rate was lowered by 10 basis points to 1.9%; Continue to make a one-year MLF of 401 billion yuan, and the winning bid rate will be lowered by 15 basis points to 2.5%. At the same time, the central bank lowered the standing loan facility interest rate (SLF) by 10 basis points. Market participants believe that the interest rate cut has exceeded expectations in both timing and magnitude, clearly releasing the signal that monetary policy is exerting its strength to support steady growth. LPR quotation is expected to go down in August, and LPR for more than five years does not rule out a larger adjustment. In addition, it is still possible to lower the standard. (wonder)
2. Key economic growth indicators slowed down in July.
On August 15th, the National Bureau of Statistics released the operation data of several major economic indicators. In July, the year-on-year performance of industrial production, investment, consumption and other indicators declined from last month, and was lower than the expectations of market institutions. Market institutions believe that the current economy is still bottoming out, and the support policy should be accelerated. It is reported that relevant departments are actively planning to implement a reserve policy to promote economic recovery. (Securities Times)
3, the national youth urban survey unemployment rate will be suspended.
On August 15th, the State Council held a press conference on the operation of the national economy in July 2023. Fu Linghui, spokesperson of the National Bureau of Statistics and director of the comprehensive statistics department of the national economy, said at the meeting that since August this year, the release of the urban survey unemployment rate of young people of different ages in China will be suspended, mainly because the economy and society are constantly developing and changing, the statistical work needs to be continuously improved, and the labor force survey statistics need to be further improved and optimized. (xinhuanet)
4. Biden urges UAW to reach a fair agreement with automobile manufacturers.
US President Biden urged the United Auto Workers’ Union (UAW) and Detroit’s three major automakers to reach a "fair agreement" and expressed their views on the significant impact of the tense negotiations between the two sides on the US economy. It is reported that the current contract between UAW and the automobile manufacturer will expire on September 14th, but there are huge differences in salary, welfare and electrification transformation. UAW is seeking to raise wages, restore pensions for new employees and reduce working hours. According to informed sources, these requirements will increase the labor costs of the three giants by more than 80 billion US dollars respectively. (Reuters)
5. The Russian central bank sharply raised interest rates by 350 basis points.
The Russian central bank sharply raised interest rates by 350 basis points to 12%, only 25 days after the previous rate hike. The Russian central bank said that the devaluation of the ruble is accelerating the transmission of prices, and inflation expectations are rising. The interest rate hike is aimed at curbing inflation risks. It is reported that Russia is also discussing the resumption of capital controls to curb the devaluation of the ruble. (wonder)
6. Fitch International once again warned the US banking risks.
An analyst of Fitch Ratings, an international rating giant, recently warned that the US banking industry is gradually approaching the beginning of another turmoil, and may downgrade the ratings of dozens of banks in the United States, which may even include large banks such as Chase. On the evening of the same day, the three major US stock indexes collectively opened lower and went lower. (Sina Finance)
7. This year, China has reduced production by 390,000 vehicles due to lack of cores.
According to the latest data of AutoForecast Solutions(AFS), a data forecasting company in the automotive industry, as of August 13th, due to the shortage of chips, the global automotive market has reduced production by about 1,932,300 vehicles this year. Among them, China’s automobile market has reduced production by nearly 390,000 vehicles, accounting for about 20% of the global total. AFS predicts that by the end of this year, the global automobile production reduction will climb to about 2.41 million. According to the latest estimate of AFS, last week alone, the global automobile market reduced production by 80,710 vehicles due to lack of cores. (Geshi Automobile)
8. In 2024, 20,000 charging infrastructures will be built in rural Zhejiang.
On August 15th, the Zhejiang Development and Reform Commission and the Provincial Energy Bureau recently issued the "Top Ten Actions for New Energy Vehicles in Zhejiang Province to Go to the Countryside". The List includes ten actions, including the promotion of rural charging infrastructure in the future, the transformation of charging infrastructure in beautiful towns, and the construction of charging infrastructure along highways. Among them, the List states that. By the end of 2024, the number of public charging infrastructures in rural areas of the province reached 20,000. (First Electric)
9. Lei Jun’s annual speech was accused of "insufficient steam content"
The high-profile Lei Jun’s annual speech ended. After more than three hours of speech, Lei Jun talked about entrepreneurship from studying, and from dreams to growth. Xiaomi’s folding screen mobile phones, tablet computers, robot dogs and other products took turns to appear, but the Xiaomi car business that was concerned was rarely mentioned. From 2021, Xiaomi announced a high-profile investment of $10 billion in 10 years to build a car. Up to now, the goal of mass production of Xiaomi Automobile in the first half of 2024 may be less than half a year. Netizens expect Lei Jun to release eggs in the last link of the speech "One More Little Thing", but only wait for the second generation robot dog "Iron Egg". The netizen asked in expectation: Where is the car? (Geshi Automobile)
10. Hundreds of new energy vehicles were selected for the 374th batch of new cars.
On August 14th, the Ministry of Industry and Information Technology publicized the Announcement of Road Motor Vehicle Manufacturers and Products (the 374th batch). According to statistics, there are 455 models of 177 enterprises applying for new energy automobile products, including 141 enterprises with 391 models of pure electric products, 39 models of 23 enterprises with products and 25 models of 13 enterprises with products. A number of heavy new energy vehicles appeared in the announcement. These include highly concerned Zhijie S7, Song L, Jiyue 01, Yinhe E8, BMW i5, Qiyuan Q05, Starlight, EV5, Zhiji LS6, OPTIQ four-wheel drive version, Xingyue ES, QX PHEV, 5, Raptors, Changan Qiyuan A05, Changan Qiyuan A06, Jianghuai Ruifeng E4, SAIC Datong MILA1, etc. First Electric is sorting out the relevant information of these heavy new cars, and the details will be released one after another. (First Electric)
11. It means that a new data center will be established.
Foreign media reported that Tesla said it would build a new data center. Tesla is recruiting employees for this purpose and snapping up some existing data centers. The data center industry is currently huge, with a market scale of over $250 billion. Most of the world’s largest companies (known to consumers for other products) such as Amazon Cloud Technology, microsoft azure Service, Cloud Platform and Meta Platforms are involved. Now, Tesla has also begun to get involved in the data center business. It is reported that Tesla has released a new recruitment notice, and the position for recruitment is "Sr. Engineering Program Manager (Data Center)". (Geshi Automobile)
12. Tesla set up a 20-person FSD operation team in China.
According to informed sources, Tesla deployed the fully automatic driving scheme FSD into China, and initially planned to set up a local operation team of about 20 people. At the same time, Tesla also tried to set up a data annotation team with a scale of about 100 people in China to prepare for training the algorithm of FSD. (36Kr)
13. Tesla launched a new version of /X and was accused of price reduction in disguise.
Tesla official website shows that Tesla has launched the Model S and the Model S with shorter cruising range and lower price in the United States, which comes at a time when the company continues to focus on reducing costs and giving priority to sales growth. Among them, Tesla’s new Model S and Model X "Standard Range" versions are priced at $78,490 and $88,490 respectively, which is about 10% lower than the previous version with the lowest price (that is, $10,000) and can be delivered from September to October 2023. The cruising range of both cars is much lower than the basic version. (Reuters)
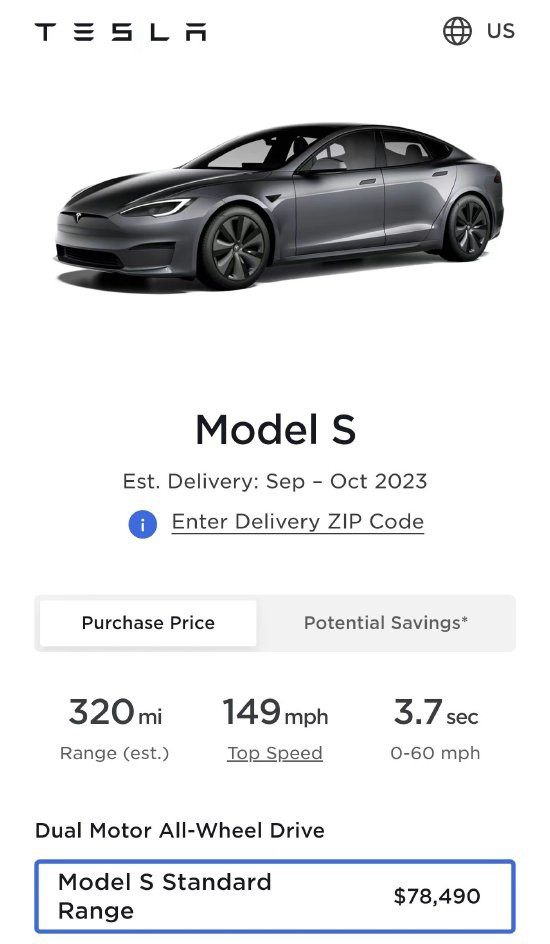
14, the first version of the opening of intelligent navigation in Beijing, Chongqing and Hangzhou city.
It was learned from the official of Polar Fox Automobile that its pioneering version of Polar Fox Alpha S opened NCA (Urban Intelligent Pilot) in Beijing, Chongqing and Hangzhou, which was fully open to users. Previously, the NCA of Extreme Fox Auto City was opened in Shenzhen, Shanghai and Guangzhou. The official said that the cumulative intelligent driving mileage of Extreme Fox Alpha S was 1 million kilometers, and the longest driving mileage of a single NCA was 1931 kilometers, and the accuracy of parking space identification reached 96%. (Netease Auto)
15, the more detailed information disclosed in 01, the more intelligent armed to teeth.
Geely Holding Group and Baidu jointly built the first car, Jiyue 01, which attracted much attention. First Electric got more detailed information about the car at the first time. There are three versions of this model, namely Ferrous lithium phosphate+single motor (CLTC battery life or 550km),+single motor, ternary lithium battery+dual motor; The price of small battery single motor version will be at the level of 250 thousand yuan, facing the competition directly; Extreme Yue 01 and another brand under Geely are produced in the same line, and 80% of the components in the chassis structure are the same; In terms of intelligence, the Extreme Yue 01 is equipped with 31 sensors, including 2 laser radars located under the headlights, and all three versions have this configuration. Backed by Baidu Group, Tuzhijia and ERNIE Bot Big Model will be fully used, and Extreme Yue 01 looks worth looking forward to. (First Electric)
16. Geely Yinhe L6 has arrived at the store nationwide.
Geely Yinhe New Energy officially announced that Geely Yinhe L6 has arrived at the store nationwide and can be evaluated at any time. Geely Yinhe K6 is equipped with Yinhe NOS intelligent system and a new generation of Raytheon 8848 power system, which supports four modes: pure electricity, extended range, intelligence and performance. It is a cost-effective intelligent electric vehicle that Geely places great hopes on. (First Electric)
17. BMW i5 passed the declaration and came standard with air springs.
Last week, the official information picture of BMW i5 was released. On August 14th, BMW i5 appeared on the 374th filing list of the Ministry of Industry and Information Technology, which means that BMW i5 has passed the declaration. It is reported that the BMW i5 Travel Edition codenamed G61 BEV came together. According to people close to BMW, there are still uncertainties in the production of the i5. There are various indications that the i5 will not come to us so soon. According to the catalog information, this model is i5 eDrive 35L with a body size of 5175×1900×1520mm and a wheelbase of 3105 mm. It uses a 250kW motor made by ZF electric drive in Shenyang factory and uses ternary lithium batteries. The whole vehicle was built by BMW Brilliance Shenyang factory in China. (First Electric)
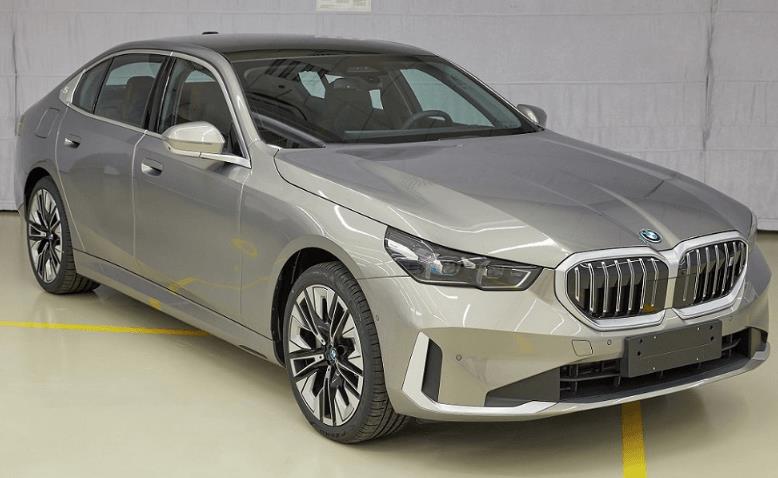
18. BYD Song L reported that it is expected to be listed in the fourth quarter.
A brand-new compact BYD appeared in the announcement of the 374th batch of new car declaration by the Ministry of Industry and Information Technology, that is, BYD Song L, which had previously exhibited the concept model at the Shanghai Auto Show, and this model is expected to be released in the fourth quarter of this year. This model is a plug-in hybrid model with a maximum power of 81kW and a displacement of 1.5L Therefore, it is expected that this model will adopt the same DM-i powertrain as Song PLUS, with a total motor power of 145kW and a total motor torque of 325n m.. The price of this model is expected to be basically the same as that of BYD Song PLUS DM-i model, that is, about 160,000 yuan to 190,000 yuan. (First Electric)
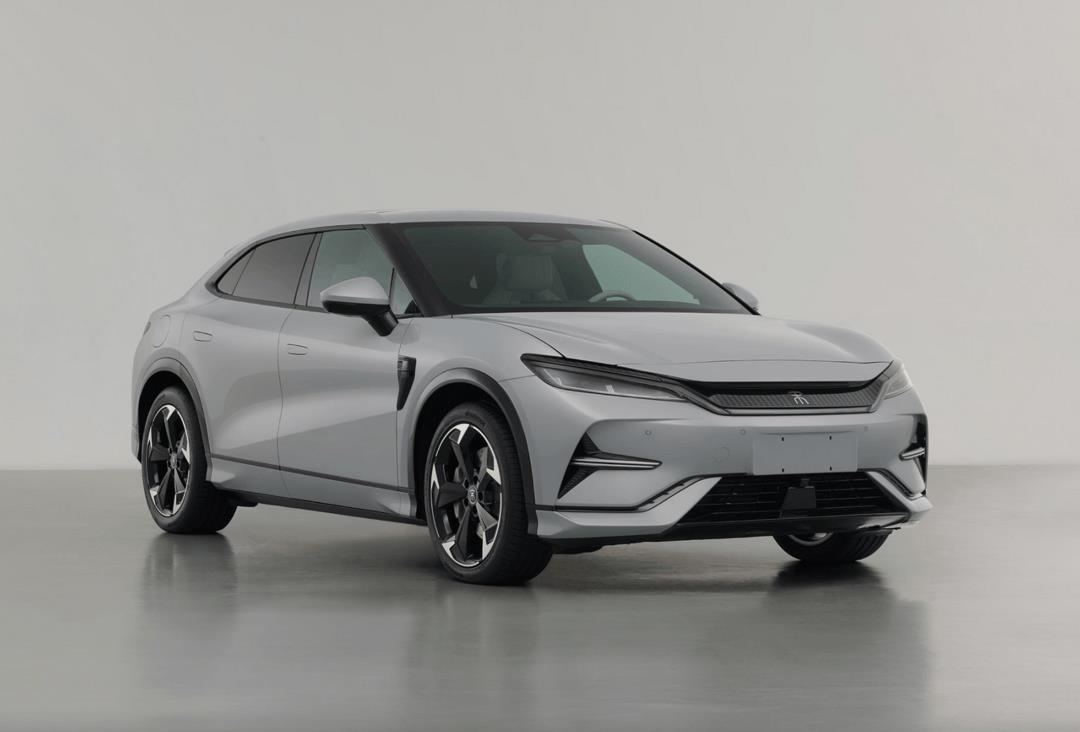
19, Wuling starlight declaration data release.
Wuling starlight, a brand-new new energy car of SAIC-GM-Wuling, appeared in the announcement of the 374th batch of the Ministry of Industry and Information Technology. At present, the declaration drawing of this model can be divided into two appearances, the plug-and-mix version of the car and the pure electric version. In terms of power, the model will be equipped with lithium iron phosphate batteries produced by Ripsek, and the maximum power of its motor is 100kW;; The hybrid version will be equipped with a 1.5L self-priming engine and motor. The maximum power of the engine is 78kW, and the maximum power of the matched motor is 75kW. In terms of price, Wuling Xingguang is still expected to take the people-friendly route as the main route. The price of hybrid models is expected to be 90,000-130,000 yuan, and the price of pure electric models is about 120,000-150,000 yuan. (First Electric)
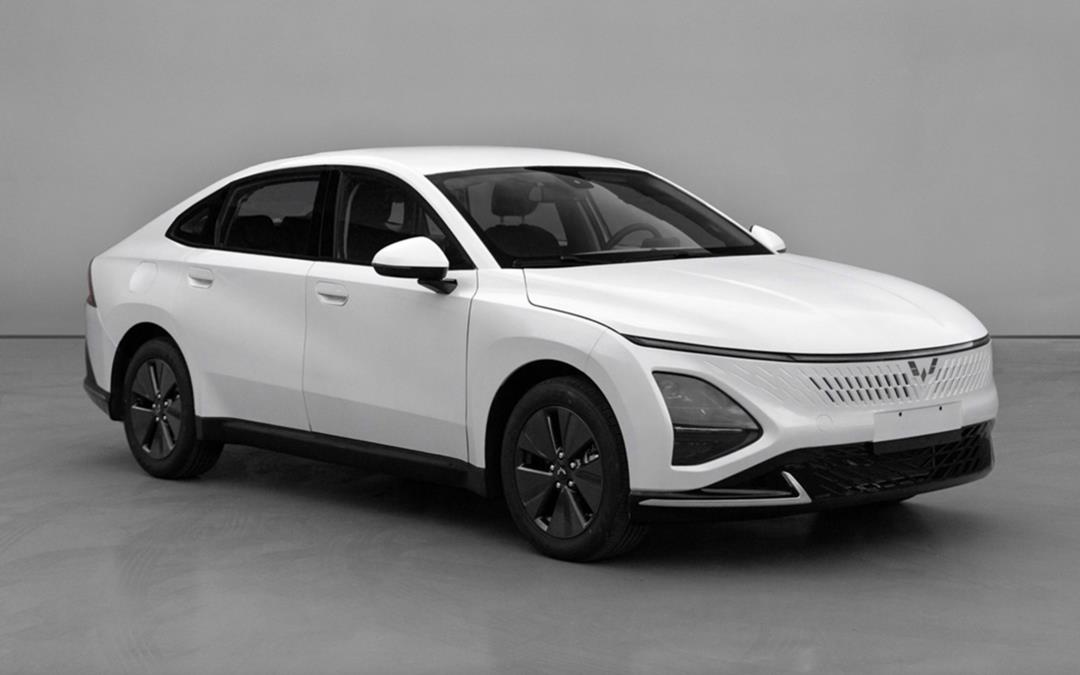
20. Changan Qiyuan A05 plug-in hybrid version passed the declaration.
Changan Qiyuan A05 plug-in hybrid version appeared in the 374th batch of new car catalogue of the Ministry of Industry and Information Technology. The size of the new car is similar to that of Chang ‘an Yida, which can be regarded as the "shell-changing" model of Yida. Under the working condition of WLTC, the new car has a pure battery life of 53 kilometers and a comprehensive fuel consumption of 4.58L per 100 kilometers, and its power performance will be better than BYD Qin Plus DM-I.. In terms of power, the new car will adopt plug-in hybrid power, in which the maximum power of the 1.5L engine is 81kW, and the driving motor will provide two kinds of high power and low power, with the maximum power of 140kW and 158kW respectively, and Ferrous lithium phosphate (China Singapore Airlines) and ternary lithium battery (Yiwei Power) will be provided, and the chassis is designed as a load-bearing body. (First Electric)
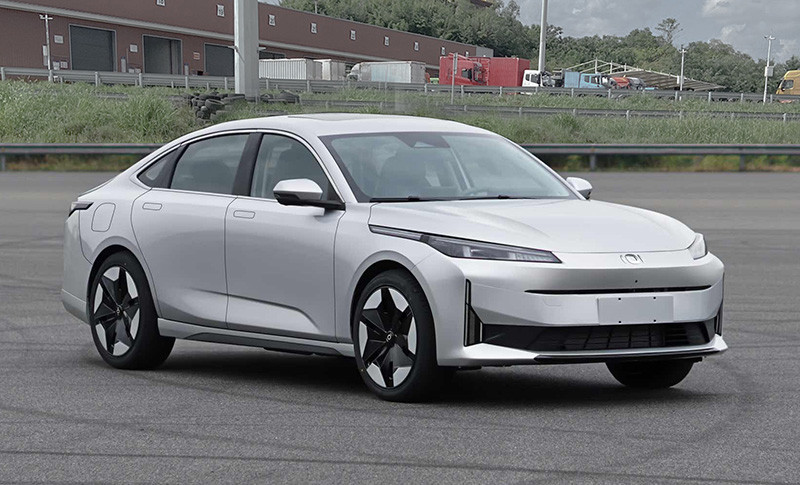
21. Changan Qiyuan’s first SUV Q05 passed the declaration.
Chang ‘an Qiyuan Q05 appeared in the 374th batch of new car catalogue of the Ministry of Industry and Information Technology. As an SUV model, the new car will be the standard Song PLUS, and the price is expected to be around 150,000.
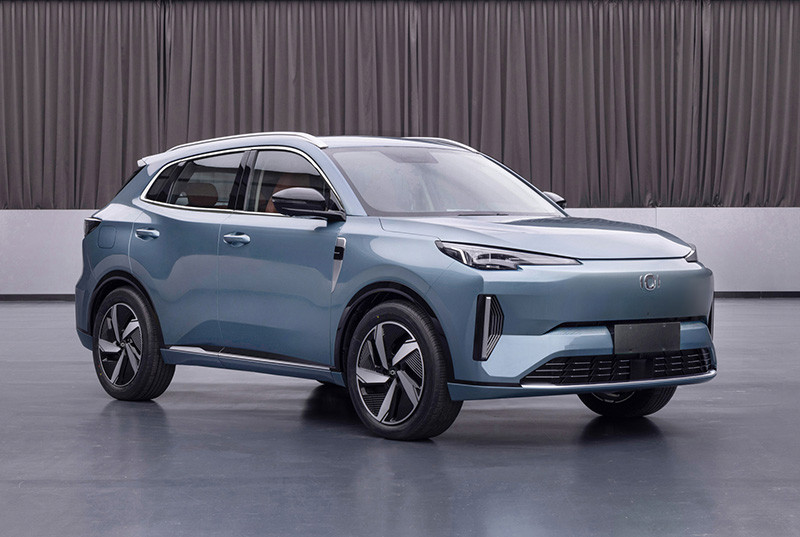
In terms of power, the new car is equipped with a hybrid system consisting of a 1.5L naturally aspirated engine and an electric motor. The maximum power of the engine is 81kW, and the peak power of the motor is 158kW. (First Electric)
22. Geely Galaxy E8 officially completed the declaration by the Ministry of Industry and Information Technology.
Geely Galaxy’s first pure electric vehicle, E8, which locates medium and large cars, was officially declared by the Ministry of Industry and Information Technology. The car body size is 5010mm/1920mm/1465mm, and the wheelbase is 2925mm. It is said that the rear end resembles Paramera. Lithium iron phosphate battery is adopted, and the publicity version is single motor version; Galaxy E8 is equipped with laser radar and other configurations, and it is expected to support high-order assisted driving scheme. The price of Galaxy E8 will be around 300,000 yuan, and it is expected to be listed in the fourth quarter. (First Electric)
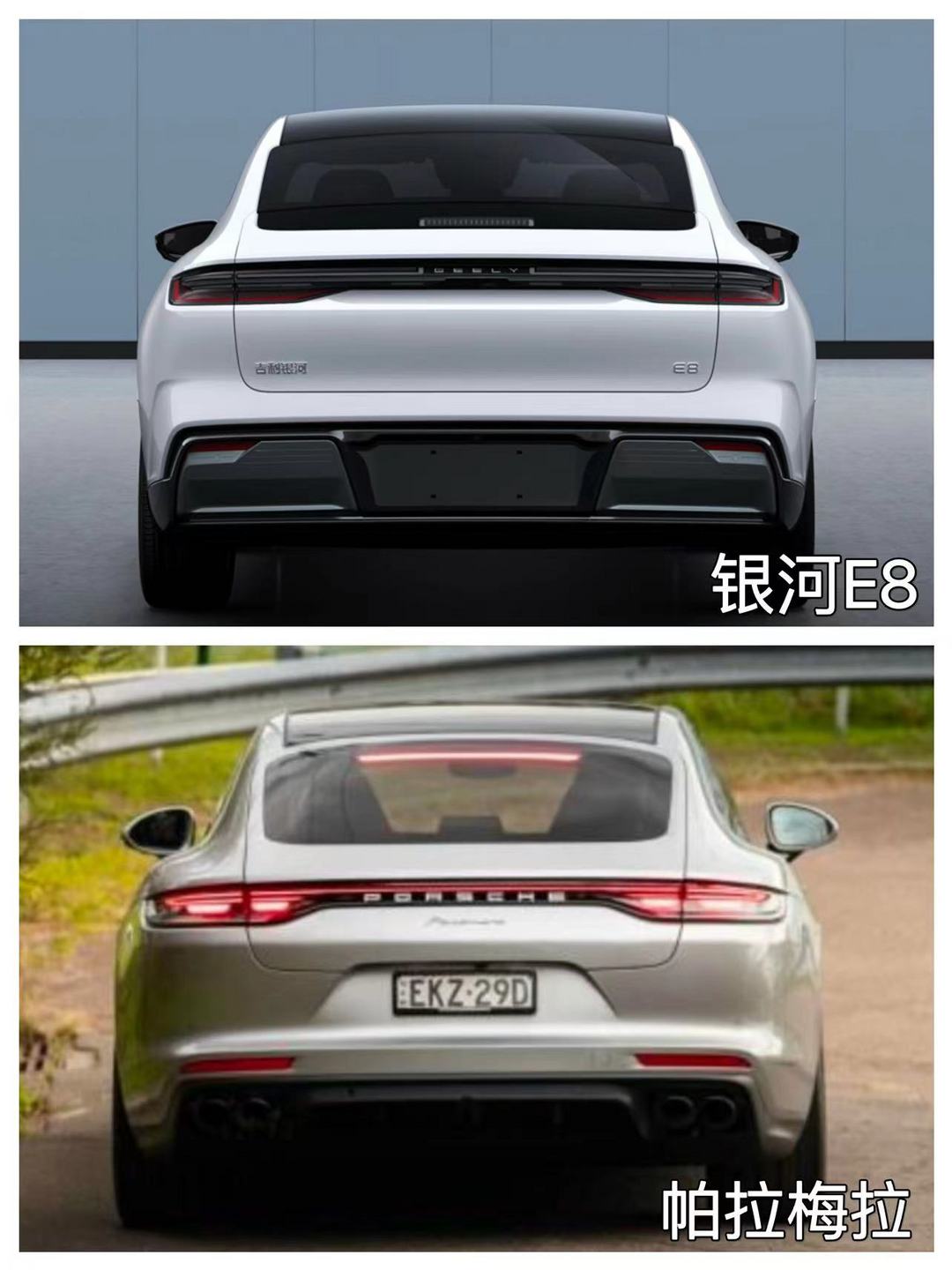
23. The first HarmonyOS 4 pure electric coupe passed the declaration.
In the 374th batch of the list declared by the Ministry of Industry and Information Technology, the first model of the Luxeed brand, Zhijie S7, jointly built with Huawei Zhixuan, was unveiled. The car is positioned as a pure electric medium and large coupe, and will be equipped with Huawei HarmonyOS HarmonyOS 4 car system, which will be released in the third quarter. According to the data, the new car will provide two power versions: single-motor two-wheel drive and dual-motor four-wheel drive. The maximum output power of the driving motor of the two-wheel drive model is 215KW, and the maximum power of the front and rear motors of the four-wheel drive model is 150 kW and 215 kW respectively. As the first pure electric coupe with HarmonyOS 4 pushed by Huawei Yu Chengdong, the market is full of expectations. (First Electric)
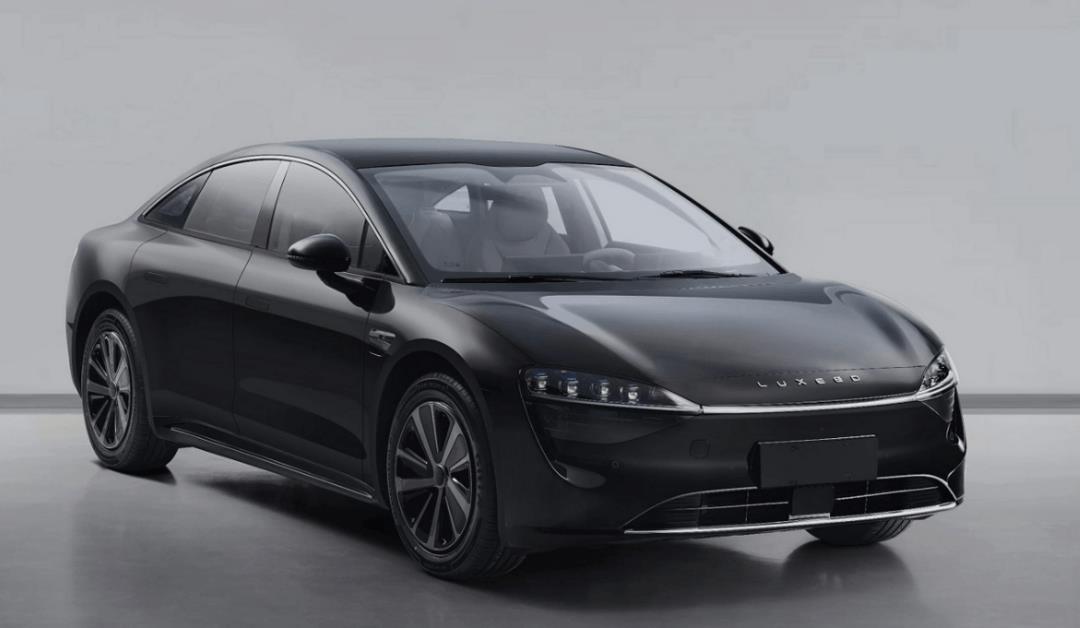
24. KIA EV5 compact SUV passed the declaration.
Kia’s compact SUV named EV5 has been declared by the Ministry of Industry and Information Technology. The concept model of this EV5 has previously appeared at the Shanghai Auto Show, and it is expected that it may be officially unveiled at the Chengdu Auto Show. This car uses the lithium iron phosphate battery of BYD’s Foday brand. Based on the E-GMP pure electric platform, it is the first model produced in China and listed in the world by Kia of yueda. According to the news, the overseas version of this model has 800V charging function, and there is also a version with a battery life of more than 700km. (First Electric)
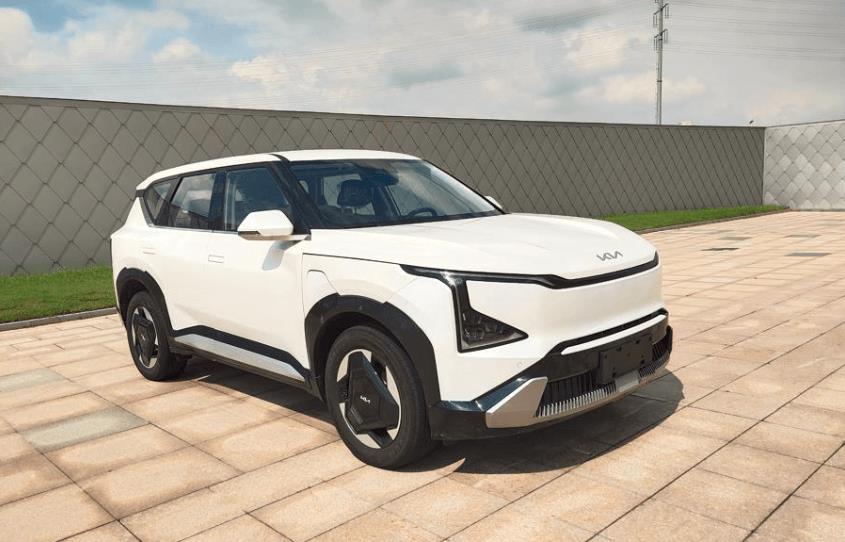
25. It is planned to electrify the entire product line in Malaysia in 2030.
Mercedes-Benz Group is targeting Malaysia as one of its target markets, and plans to electrify its entire product line in that country in 2030. Earlier this year, Mercedes-Benz became the first automobile manufacturer to launch local electric vehicles in Malaysia. Mercedes-Benz’s sales of electric vehicles in Malaysia have soared by 200%. Although the base is low, it exceeds the global growth rate of the group of about 120% in the first half of the year. (Geshi Automobile)
26, the end of the internal combustion engine complex, the first pure electric vehicle.
Lamborghini finally decided to launch its first pure electric vehicle, which will be displayed at Monterey Auto Week on August 18th. At present, Lamborghini only posted a blurred photo of the car on its social media, calling it a 100% pure electric car. According to the official introduction, this car will adopt the new platform "SSP Sport" developed by the leaders, and it is planned to be officially launched in 2028. Lamborghini said that its other three models-Aventador, Huracan and Urus-will be electrified. (IT house)
27. Version V2.0 of iFLYTEK Spark Cognitive Model was released.
Iflytek released "Version V2.0 of iFLYTEK Spark Cognitive Model". Liu Qingfeng, Chairman of Iflytek, said that judging from the comparison of the results in the industry reference test set, Spark V2.0′ s code writing ability based on Python and C++ has been highly close to ChatGPT, with the goal of formally benchmarking GPT4 in the first half of next year. (Sina Technology)
Pang Guanchen said: In preparation for the Chengdu Auto Show, we have to bring you a lot of new car information.